在建筑工程领域,钢结构设计长期面临效率低、精度不足的困境。据统计,传统设计流程中,因模型调整导致返工的比例高达40%。当行业呼唤变革时,<高效革新智能驱动3D3S钢结构设计软件领航未来建造>的出现,是否真正打破了技术瓶颈?我们通过三个核心问题展开探讨。
一、参数化建模如何颠覆传统?
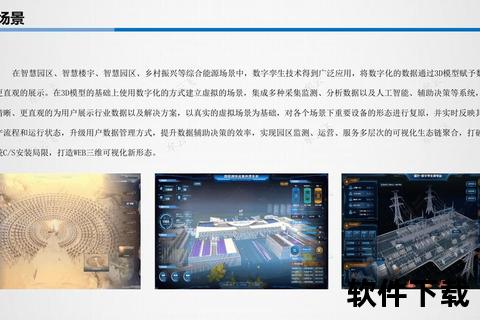
某国际会展中心项目中,设计师需在两周内完成跨度120米的异形钢架设计。借助3D3S的参数化建模功能,通过定义截面属性、材性参数和荷载组合,仅用3天便生成符合轻钢规范的结构模型。软件内置的“钢架模板生成”功能,可快速创建单跨或多跨模型,并通过“截面优选”自动匹配最优构件尺寸。这种智能化的建模方式,较传统CAD绘图效率提升3倍以上,错误率降低60%。正如上海某设计院总工所言:“过去需要反复验证的节点连接,现在通过<高效革新智能驱动3D3S钢结构设计软件领航未来建造>的智能校验功能,能即时发现并修正设计冲突。”
二、复杂形态如何精准找形?
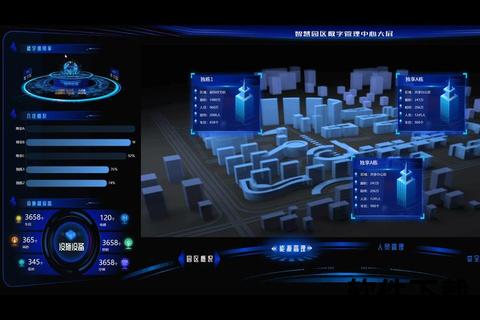
杭州某体育场的膜结构车棚设计曾让工程师头疼——既要保证膜面应力均匀,又要与下部钢架完美协同。3D3S提供的五种找形方法中,工程师选择“有限元索杆梁膜法”,将膜面与支承结构共同建模。通过设置硬边界约束、定义经纬向预张力(2.5kN/m),软件自动完成形态优化,生成满足位移协调的稳定结构。实测数据显示,该方案比传统力密度法减少用钢量12%,施工周期缩短20天。这种<高效革新智能驱动3D3S钢结构设计软件领航未来建造>特有的协同找形技术,正在重塑大跨空间结构的设计范式。
三、全流程协同怎样突破壁垒?
在深圳超高层钢结构项目中,3D3S展现了从设计到施工的全链条协同能力。通过“实体建造与绘图系统”,软件可直接导入SAP2000计算模型,生成包含螺栓孔位、焊缝尺寸的加工详图。更值得关注的是其“施工过程模拟”功能:工程师设置12个施工步,模拟钢构件吊装顺序对结构变形的影响,成功规避了3处潜在安全风险。项目负责人表示:“软件输出的数控加工数据,使构件加工精度达到±1mm,现场拼装误差控制在3‰以内。”这种数字化闭环,印证了<高效革新智能驱动3D3S钢结构设计软件领航未来建造>在智能建造领域的领先地位。
对于行业从业者,建议分三步实践革新:首先掌握软件的参数化建模核心功能(如荷载组合定义、截面优选),其次深度应用找形算法解决异形结构难题,最后打通BIM协同平台实现全流程数据流转。正如某院士在行业论坛指出:“未来五年,能驾驭智能设计工具的企业,将在钢结构细分领域获得70%以上的市场份额。”选择<高效革新智能驱动3D3S钢结构设计软件领航未来建造>,不仅是技术升级,更是开启智能建造新纪元的钥匙。