一、传统钣金工艺为何被贴上"低效"标签?

在机械制造车间,老师傅们常说:"三分手艺,七分算料。"这句行话道破了传统钣金工艺的痛点——展开计算如同在迷雾中摸索,稍有不慎就会造成材料浪费。某汽车配件厂曾因手工计算误差导致价值12万元的镀锌板报废,这样的案例在行业内并非个例。据中国机械工业联合会2024年统计,我国钣金加工企业平均材料利用率仅为78.6%,而使用智能高效能CAD钣金展开软件的企业,这一数据可提升至94%以上。这种数字鸿沟背后,正是传统工艺对人工经验的过度依赖与数字化工具的缺位形成的强烈反差。
二、一键生成展开图是纸上谈兵?
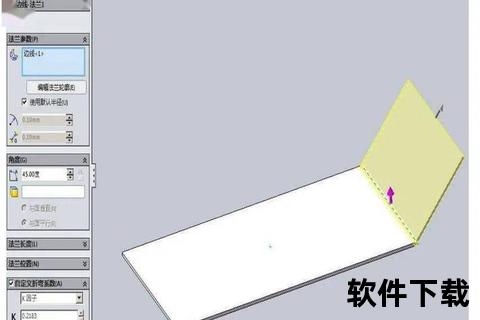
金林钣金展开软件的实践给出了有力回应。该软件将7大类140多种常见构件的展开计算封装成标准模块,操作者只需输入管径、壁厚等基础参数,系统即可自动生成带尺寸标注的三视图与展开图。以某电梯轿厢制造企业为例,过去需要3天完成的异形通风管道展开计算,现在通过软件仅需20分钟,并可直接输出DXF格式文件给激光切割机。更值得关注的是其"双标注模式":传统长度标注便于手工下料,坐标标注则适配数控设备,这种设计完美衔接了不同生产场景的需求。
三、智能补偿如何破解折弯精度魔咒?
在折弯工序中,材料回弹堪称"隐形杀手"。中望3D的折弯补偿算法通过建立材料属性数据库,将回弹量预测误差控制在±0.1°以内。其"沿线折弯"功能可自动识别折弯线走向,生成符合JIS标准的折弯工序图。某机箱制造商应用该功能后,产品装配合格率从82%跃升至98%,返工成本下降67%。SOLIDWORKS 2025新增的折弯凹口功能更是革命性突破,通过在展开图上生成物理标记,帮助操作工精准定位,将折弯对位时间缩短40%。
四、云端协同能否打通设计到制造的任督二脉?
村田机械的Videre视教软件给出了智能化解决方案。该平台将工艺参数、模具信息、操作规范等数据云端同步,在设备端以AR方式实时投射指导信息。某钣金加工中心引入该系统后,新员工培训周期从3个月压缩至2周,设备切换模具的平均时间由45分钟降至12分钟。这种数字孪生技术的应用,使得智能高效能CAD钣金展开软件一键式精准革新钣金工艺的价值链延伸至生产现场。
对于准备数字化转型的企业,建议分三步走:首先选择支持AutoCAD2004-2025版本兼容的软件确保历史数据继承;其次重点考察软件的智能补偿算法与材料数据库深度;最后通过API接口实现与MES系统的数据贯通。正如某行业专家所言:"未来的钣金车间,不是比谁家的设备先进,而是拼谁的算法更懂材料。"当智能高效能CAD钣金展开软件一键式精准革新钣金工艺成为行业标配,那些曾困扰制造业的精度之痛、效率之困,终将在数字化的浪潮中迎刃而解。