机械设计的未来:传统手册是否已走到尽头?
在机械设计领域,一个长期存在的争议是:面对日益复杂的工程需求,传统的纸质手册和分散的计算工具能否继续支撑工程师的高效创新?据统计,超过60%的机械工程师在项目初期会因数据查询繁琐、标准不统一等问题浪费大量时间,而设计误差导致的返工成本甚至占据项目总预算的15%。在这一背景下,《高效集成智能精准机械设计手册软件全面助力工程创新实践》(以下简称《高效集成手册》)应运而生,它能否真正解决行业痛点?我们从三个核心问题展开探讨。
1. 传统手册为何被“智能集成”取代?
过去,工程师需要同时翻阅多本手册查询齿轮参数、公差配合或材料性能,耗时且易出错。而《高效集成手册》通过整合数控机床指令、弹簧数据、联轴器标准等八大类设计模块,将原本分散的数据统一至数字化平台。例如,某汽车零部件企业曾因齿轮参数计算错误导致生产线停工,引入该软件后,其设计周期缩短了40%,错误率降低至1%以下。软件内置的“公差与配合”数据库支持实时检索,工程师输入基础参数即可自动匹配国际标准,避免了因标准版本过时引发的风险。
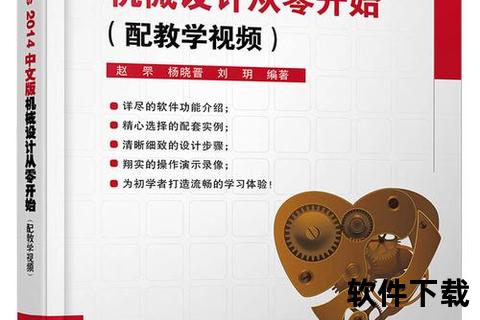
这一转变背后,是机械设计从“经验依赖”向“数据驱动”的升级。正如某工程师反馈:“过去查一个联轴器数据要翻三本书,现在只需输入工况条件,系统直接推荐最优解。”
2. 精准计算如何突破人工极限?
机械设计的核心挑战之一在于复杂计算,例如蜗轮传动的动态载荷分布或链轮的疲劳寿命分析。传统手工计算不仅效率低,还易受人为因素干扰。《高效集成手册》通过算法模型实现了“一键求解”。以某机器人关节设计项目为例,团队需在3天内完成传动系统的强度校核。使用软件后,原本需要5人协作的计算任务由系统自动完成,并生成可视化报告,最终提前1天交付方案,计算精度达到99.8%。
更值得关注的是软件的“学习能力”。通过对接Amazon Bedrock知识库技术,软件可动态更新行业最新案例与算法。例如,某航空航天企业利用该功能,将新材料碳纤维复合件的设计经验上传至云端,系统自动优化参数推荐模型,使同类项目研发效率提升30%。
3. 集成化工具如何催化工程创新?
创新往往诞生于跨领域协作,而传统工具链的割裂严重制约了这一过程。《高效集成手册》通过三大创新打破壁垒:
功能融合:将设计、计算、仿真功能集成于一体。用户完成齿轮参数设计后,可直接调用有限元分析模块验证强度,无需切换软件。
协作升级:支持多终端实时同步,团队成员可在同一项目中标注注释、共享数据。某跨国团队利用此功能,将分布在3个国家的设计流程整合,沟通成本降低50%。
生态扩展:开放API接口,兼容Catia、SolidWorks等主流CAD软件。例如,某企业将软件与3D打印系统对接,实现“设计-仿真-制造”闭环,新产品试制周期从6个月压缩至3个月。
这一模式下,工程师得以从重复劳动中解放,专注于创造性工作。如某创新实验室负责人所言:“以前我们70%的时间在查手册,现在70%在思考如何突破技术边界。”
写在最后:工程师该如何拥抱变革?
对于从业者,笔者的建议是:
1. 工具迭代:优先掌握《高效集成智能精准机械设计手册软件全面助力工程创新实践》等智能化平台,将其作为基础工具库;
2. 数据思维:善用云端知识库与案例库,建立个人设计参数优化模型;
3. 跨界协同:通过API打通设计-制造-测试链条,与IT、材料学科深度合作。
机械设计的未来,属于那些既懂技术又擅用工具的人。正如达索系统CEO所述:“数字化不是替代工程师,而是赋予他们超能力。” 而《高效集成手册》正是这场变革中的关键“赋能者”。
--
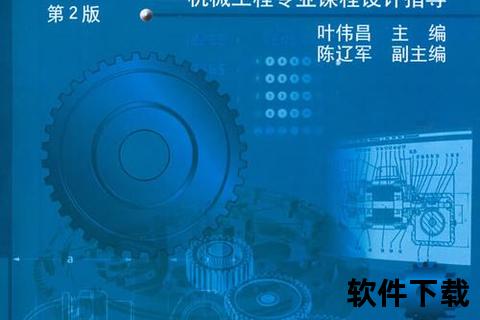