1. 传统组态软件为何难以支撑智能工厂?
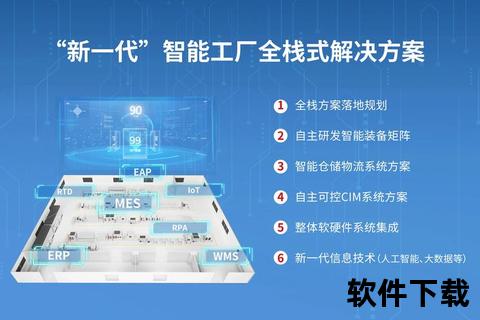
在浙江某汽车零部件制造厂,技术总监李明曾面临一个尴尬局面:生产线上的设备报警后,工程师需要手动调取5个不同系统的数据才能定位故障,平均处理时间长达2小时。这暴露了传统工业组态软件的致命短板——数据割裂、响应滞后。据统计,2022年我国制造业因设备停机导致的损失超过4000亿元,其中60%与软件系统协同能力不足直接相关。
创新升级工业组态软件高效驱动智能制造全场景互联的解决方案,正在改变这一局面。例如,德国西门子推出的MindSphere平台,通过统一数据接口整合设备、ERP、供应链系统,使某电池工厂的故障响应时间缩短至15分钟。这印证了一个趋势:只有打破“信息烟囱”,才能释放智能制造的真正潜力。
2. 创新升级如何打通数据孤岛?
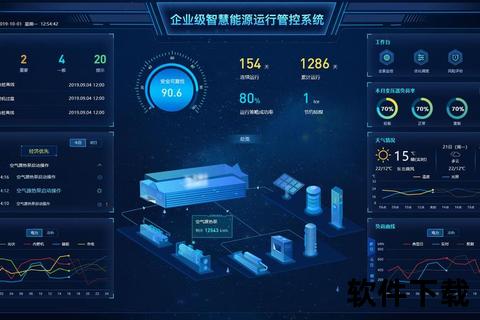
山东某化工厂的转型案例极具代表性。该企业原有DCS、MES、能源管理系统分别来自三家供应商,数据互通需要人工导出Excel表格。引入施耐德电气的EcoStruxure平台后,组态软件将异构系统数据流统一映射,使工艺优化周期从14天压缩到3天。数据显示,这种创新升级工业组态软件高效驱动智能制造全场景互联的模式,可使设备综合效率(OEE)提升23%-35%。
更值得关注的是,新一代软件开始融合数字孪生技术。三一重工在北京的“灯塔工厂”中,通过树根互联的根云平台创建产线数字镜像,实时模拟设备运行状态,成功将产品不良率从1.8%降至0.6%。这种虚实融合的数据处理能力,正是传统系统难以企及的。
3. 全场景互联如何实现降本增效?
广东某电子制造企业的实践揭示了全场景互联的经济价值。该企业原有仓储、质检、物流环节存在10%的产能浪费,使用研华科技的WISE-Studio组态软件后,通过RFID和视觉识别技术实现物料自动追踪,每年节省成本1200万元。这种创新升级工业组态软件高效驱动智能制造全场景互联的部署,本质上重构了生产关系的连接方式。
跨行业应用同样验证了其普适性。在食品行业,伊利集团采用华为云工业智能体,将2000+冷链车辆的温湿度数据与生产计划联动,使库存周转率提高18%;在钢铁领域,宝钢的智慧高炉系统通过组态软件集成8000多个传感器数据,降低能耗12%。这些案例表明,全场景互联正在从概念验证转向规模落地。
对于计划数字化转型的企业,建议分三步走:首先评估现有设备的协议兼容性,优先选择支持OPC UA、MQTT等通用协议的组态软件;其次从能耗管理、质量追溯等痛点场景切入,选择包含AI算法的平台型产品;最后建立数据治理体系,确保从设备层到决策层的信息贯通。正如海尔卡奥斯平台的应用实践所示,那些在2023年完成组态软件升级的企业,其订单交付周期平均缩短了26%——这或许就是智能制造时代的入场券。